Safety First.
At T&K Roofing, safety isn’t just a requirement, it’s the foundation of everything we do.
From our crew members to our clients, we take precautions to ensure every job is completed with the highest standards of care and professionalism.
Through rigorous training, top-tier equipment, and a commitment to industry best practices, we foster a work environment where quality craftsmanship and safety go hand in hand. By implementing forward-thinking policies and proactive safety measures, T&K goes Beyond the Roof to protect our team and partners.
To uphold these standards, we employ a full-time Safety Coordinator who conducts daily jobsite inspections and collaborates with all levels of construction personnel to ensure safety is integrated into every phase of the project.
Safety Program Highlights.
100% of T&K Employees:
- Are required to complete First Aid, Blood Borne Pathogen training
- Are required to carry a current OSHA 10-hour card
- Are subject to pre-employment drug testing and screening, random monthly drug testing and post-accident drug testing
New Employees Receive:
- New hire safety training
- Qualification for Union provided apprenticeship training in the first year of employment
- OSHA 10 hour training within 9 months of employment
- Orientation training including fall protection and all general safety training prior to assignment to a roofing or sheet metal crew
- Pre-employment fit screen testing prior to orientation
Jobsite Safety Inspection Program:
- Jobsite safety plan created for each individual project
- Daily safety checklists completed by foreman and assigned crew members
- Periodic safety inspections are performed by:
-
- T&K Safety Coordinator
- T&K Project Managers
- T&K Superintendents
- Insurance Safety Inspector
- Insurance Workers’ Comp Safety Inspector
- CNA Insurance Safety Inspector
Safety Recognition
MRCA Midwest Roofing Contractors Association
Gold Level Safety Award
(Highest achievable at the time)
2014 & 2015
Platinum Level Safety Award
(Highest achievable)
2016-2024
ILLIOWA Construction Labor Safety Impact Award
2008 – 2024
Key Safety Indicators
We take pride in maintaining a superior Experience Modification Rate (EMR)—a key industry benchmark for workplace safety. A lower EMR translates to fewer incidents, lower insurance costs, and a safer job site for both our team and our clients.
These indicators are a testament to our unwavering commitment to safety!
Year | EMR | Lost Work Day Frequency Rate | Recordable Case Frequency Rate |
2016 | 0.89 | 0.00 | 0.00 |
2017 | 0.65 | 0.00 | 0.00 |
2018 | 0.7 | 0.00 | 0.00 |
2019 | 0.68 | 0.00 | 0.00 |
2020 | .70 | 0.00 | 0.00 |
2021 | .67 | 0.00 | 0.00 |
2022 | .69 | 0.00 | 0.00 |
2023 | .69 | 1.25 | 1.25 |
2024 | .71 | 0.00 | 0.00 |
2025 | .71 |
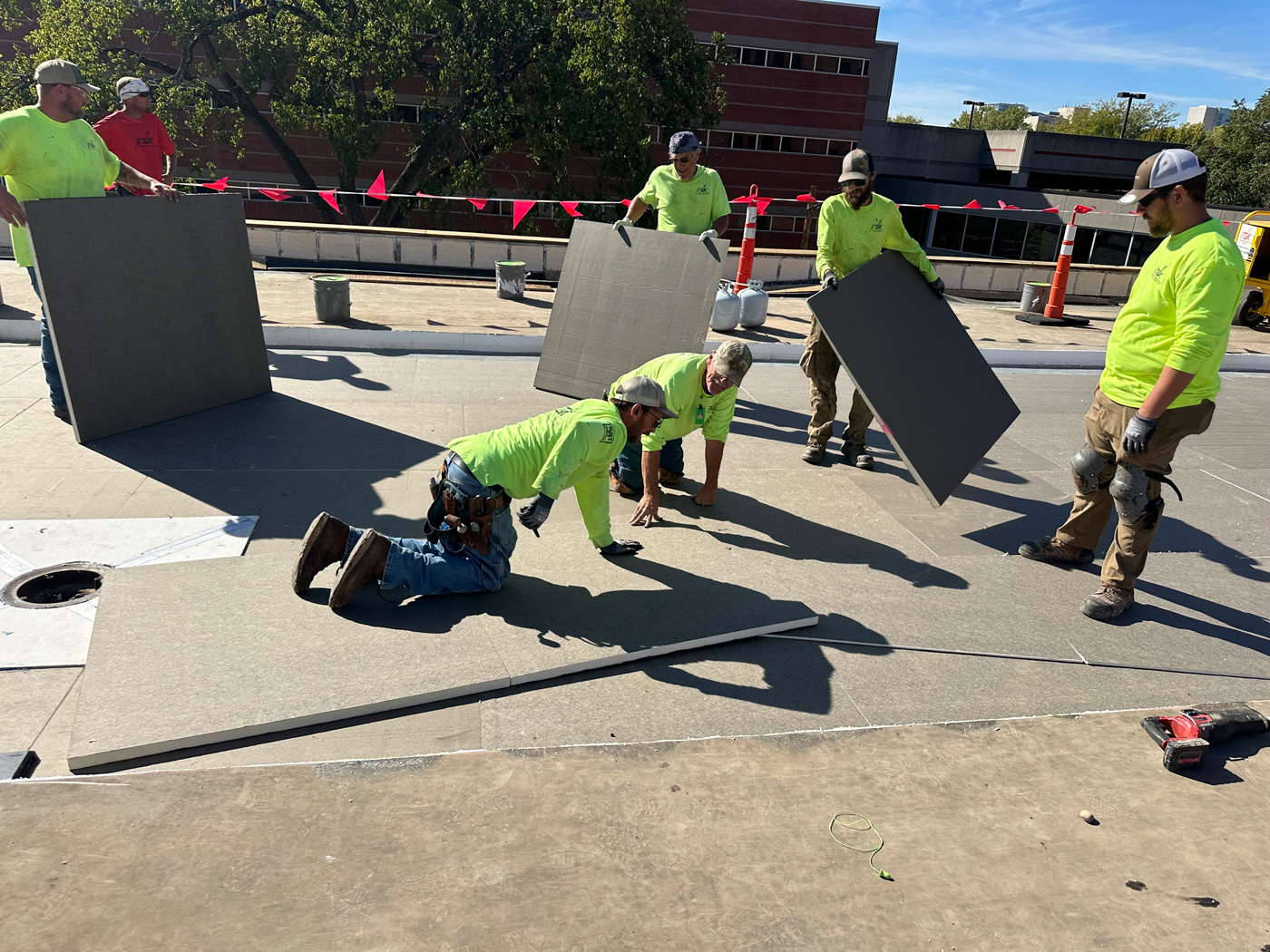
Safety Meeting Structure
Toolbox talks are held weekly, or more often as required to not only comply with project requirements, but update field staff on current safety obstacles they will be facing in a timely manner.
Monthly company-wide safety meetings are mandatory for all employees. These meetings provide a platform for safety collaboration, allowing us to identify areas for improvement and celebrate safety wins